全泥氰化—逆流洗滌—炭液法成功應(yīng)用于鑫海某金礦改建項(xiàng)目
2014-11-03 來(lái)源:鑫海礦裝 (15552次瀏覽)
已復(fù)制微信號(hào),添加好友,獲取廠(chǎng)家報(bào)價(jià)!
鑫海承攬此金礦改建項(xiàng)目,原選礦工藝為全泥氰化-炭浸工藝,由于開(kāi)采方式由原來(lái)地采改為露采,含泥量達(dá)到了15%以上,使得浸出周期變長(zhǎng),處理量被限制,選礦回收率降低,生產(chǎn)成本變高,因此該金礦亟需改變工藝,降低成本。
鑫海承包此改建項(xiàng)目后,針對(duì)該金礦現(xiàn)有設(shè)備及面臨難題,決定采用全泥氰化—逆流洗滌—炭液法工藝進(jìn)行試驗(yàn),因?yàn)樵摴に噷?duì)入浸礦石粒度的要求比全泥氰化—炭浸工藝粗,因此處理量大,是直接解決該金礦難題的良好方法。
全泥氰化—炭浸工藝存在的問(wèn)題
該工藝要求的入浸礦石粒度細(xì),為-200目占85%,而目前該金礦選廠(chǎng)的露采粒度粗,使球磨機(jī)處理量受到限制,導(dǎo)致整個(gè)金礦廠(chǎng)處理量下降,選礦噸礦成本增大;其次,炭浸工藝的炭磨損嚴(yán)重,根據(jù)鑫海選礦研究院的測(cè)試,磨損達(dá)到120g/t,金屬量損失嚴(yán)重,使得選廠(chǎng)整體經(jīng)濟(jì)效益不佳。
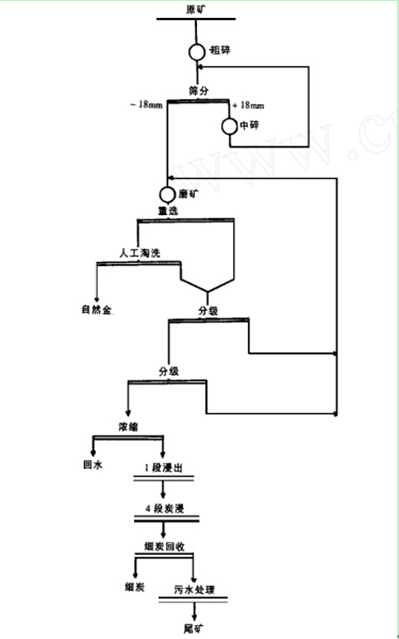
該金礦選廠(chǎng)的全泥氰化-炭浸工藝
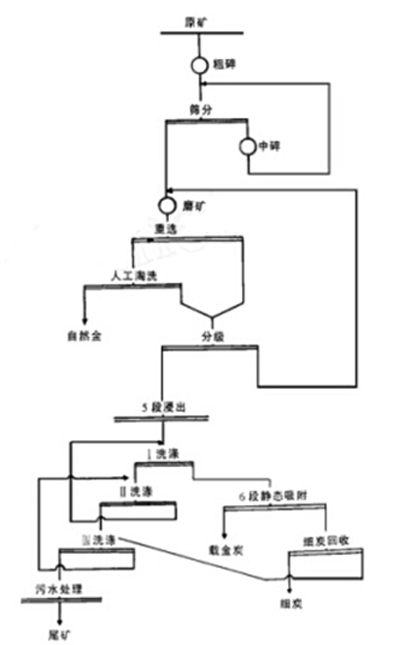
全泥氰化—逆流洗滌—炭液法試驗(yàn)結(jié)果
鑫海選礦研究院設(shè)計(jì)的此選礦工藝采用控制分級(jí)和浸前濃密,此工藝易于出現(xiàn)的問(wèn)題是因入浸礦石粒度粗、濃度低而導(dǎo)致的流程不暢、浸出率低等現(xiàn)象。但是鑫海研究院的試驗(yàn)結(jié)果表明:
1、入浸礦石粒度在一定范圍內(nèi)變化,浸出率不受影響。礦石粒度有-200目55%到-200目85%對(duì)浸出率影響均不大。
入浸礦石細(xì)度(-200目)% | 原礦金品位/g | 尾渣金品位/g | 金浸出率/% |
56.90 | 1.662 | 0.155 | 90.67 |
65.58 | 1.908 | 0.176 | 90.78 |
74.21 | 1.803 | 0.166 | 90.79 |
80.75 | 1.509 | 0.142 | 90.59 |
試驗(yàn)室對(duì)得出的入浸礦石粒度與浸出率關(guān)系
2、只要攪拌強(qiáng)度夠,礦漿將不會(huì)出現(xiàn)分層現(xiàn)象,流程暢通。
3、因該礦礦石性質(zhì)簡(jiǎn)單,浸出速度極快,因此礦漿濃度小,對(duì)浸出效果影響不大。
工藝指標(biāo)對(duì)比
工藝 | 上限處理量 | 原礦金品位 | 入浸礦石細(xì)度(-200目)% | 尾渣金品位/g | 金浸出率/% | 洗滌率/% | 選礦回收率/% | NaCN消耗/kg | 電耗/kw | 炭耗/kg | 鋼耗/kg |
全泥氰化-炭浸工藝 | 540 | 1.628 | 85 | 0.180 | 88.94 | | 87.16 | 0.45 | 25.79 | 0.12 | 1.85 |
全泥氰化-逆流洗滌-炭液法 | 800 | 1.729 | 65 | 0.181 | 89.53 | 99.0 | 86.86 | 0.35 | 16.94 | | 1.25 |
從對(duì)比可以看出,兩種工藝選礦回收率基本一致,但是按照鑫海選礦研究院對(duì)成本的計(jì)算,全泥氰化—逆流洗滌—炭液法工藝較全泥氰化—炭浸工藝要減少15.06元/t,按一年工作日330d計(jì)算,年可多創(chuàng)造效益300余萬(wàn)元。
在對(duì)該炭漿廠(chǎng)進(jìn)行工藝改造后,在實(shí)際生產(chǎn)中基本達(dá)到試驗(yàn)時(shí)的數(shù)據(jù),在入浸礦石粒度-200目65%時(shí),浸出率達(dá)到89.53%,選礦回收率86.86%,與之前全泥氰化—炭浸工藝的回收率基本一致,但是球磨機(jī)生產(chǎn)能力增加了260t/d,為該金礦炭漿廠(chǎng)節(jié)約了成本,創(chuàng)造了效益。